Why Anchor Harvey?
With more than a century of metal forming experience across a variety of industries, Anchor Harvey is redefining what customers expect from a forging supplier with our expert approach to problems-solving, data-driven process control, and quality assurance. Our innovative team has the knowledge, experience, data, and forward-focused solutions to develop practically any forging solution.
We’re ready to be your trusted end-to-end metal component manufacturing partner.
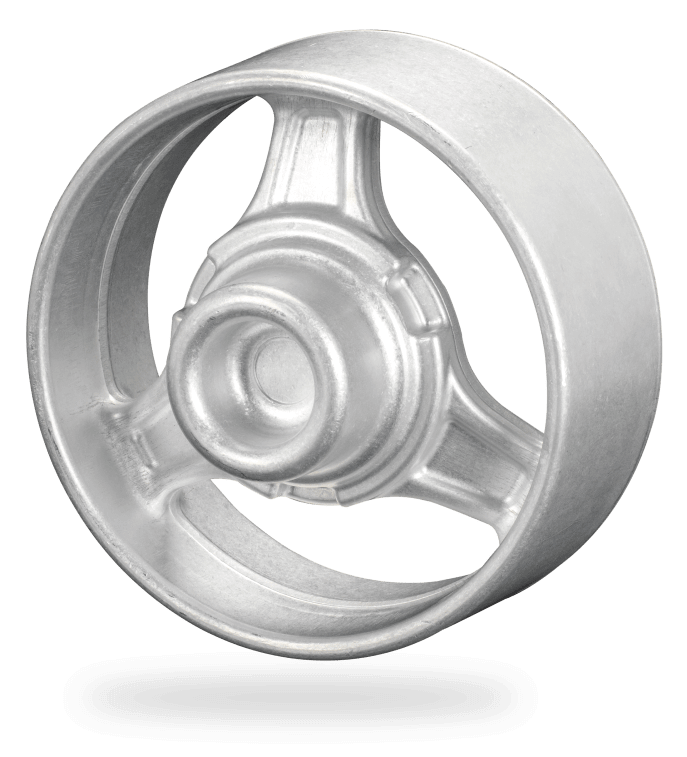
Why Anchor Harvey?
With more than a century of metal forming experience across a variety of industries, Anchor Harvey is redefining what customers expect from a forging supplier with our expert approach to problem-solving, data-driven process control, and quality assurance. Our innovative team has the knowledge, experience, data, and forward-focused solutions to develop practically any forging solution.
We’re ready to be your trusted end-to-end metal component manufacturing partner.
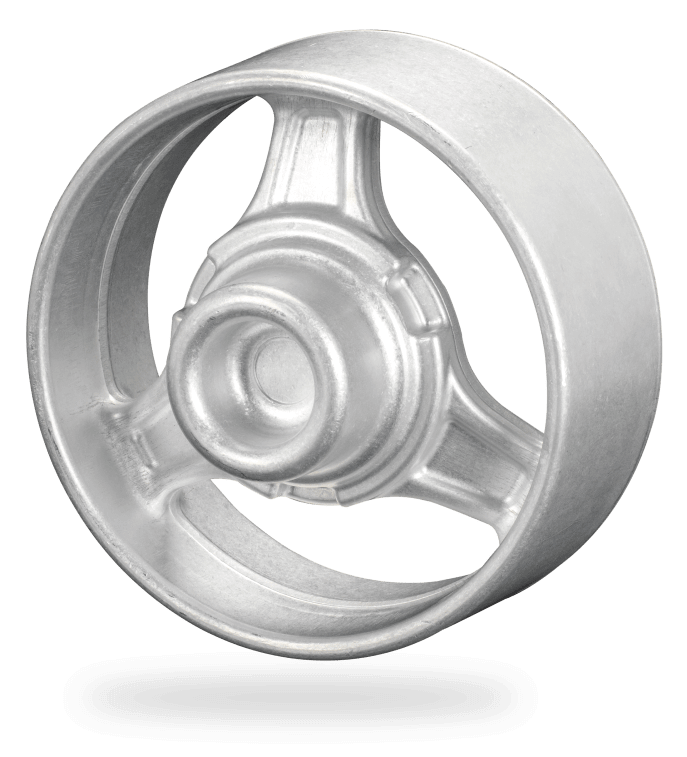
Equipment & Capabilities
Precision, Consistency, and Unmatched Detail
Bringing together deep industry knowledge, forging expertise, and innovative solutions, Anchor Harvey provides the highest quality forged aluminum products with state-of-the-art equipment and capabilities – providing optimal results for our customers.
Forged Products GALLERY
INSIGHTS & EDUCATION
Featured Capabilities
Featured Capabilities
CAREERS